The Ultimate Guide to Motorcycle Helmet Materials
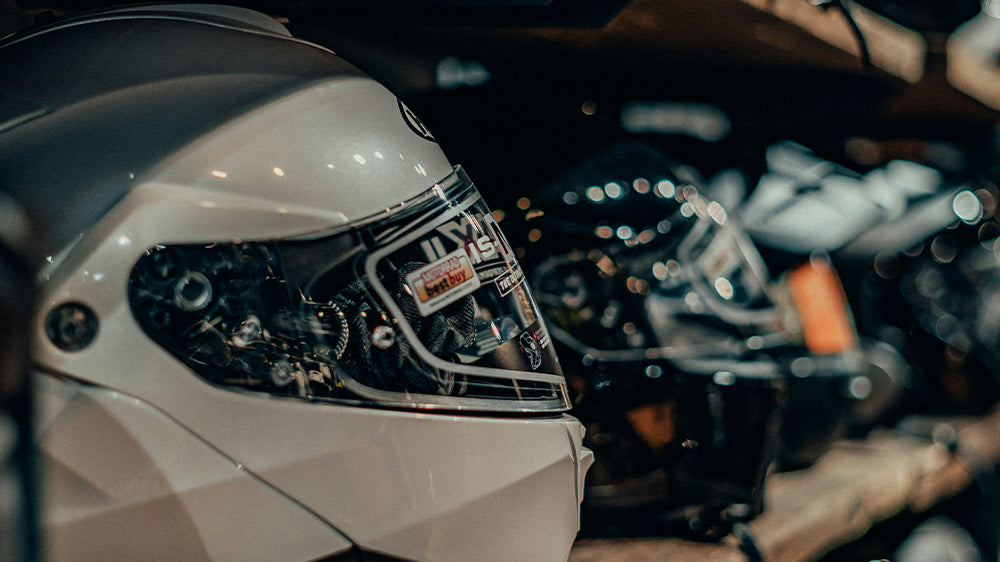
Choosing the right motorcycle helmet material is crucial for rider safety and helmet performance. High-quality materials can significantly reduce the risk of injury from accidents by absorbing and distributing impact forces more effectively. Moreover, the choice of materials affects the helmet's weight, comfort, and durability, directly influencing rider experience. Advanced materials like carbon fiber, fiberglass, and polycarbonate offer a balance of strength, weight, and resistance to impact, setting the foundation for helmets that protect and enhance the joy of riding. This makes understanding helmet materials an essential aspect of selecting the right gear for safety and performance on the road.
Understanding Helmet Safety Standards
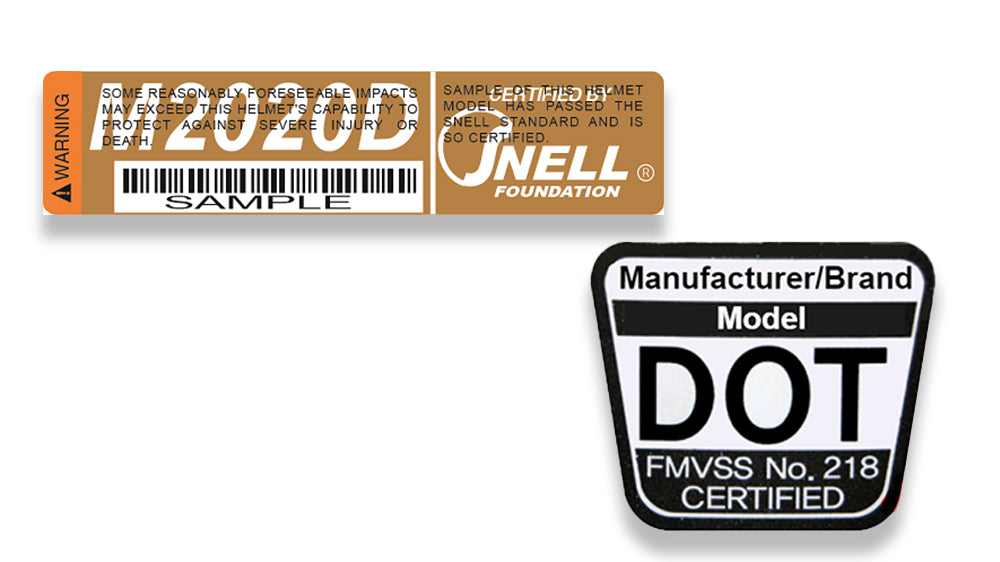
Understanding helmet safety standards is essential for selecting a helmet that not only meets legal requirements but also provides optimal protection in the event of a crash. In addition to the DOT (Department of Transportation) and ECE (Economic Commission for Europe) standards, two other critical benchmarks in helmet safety are the SNELL and FIM standards, each with unique criteria and testing protocols.
SNELL Standards: The SNELL Memorial Foundation sets one of the most stringent helmet safety standards. Unlike DOT, which is a mandatory standard, SNELL certification is voluntary and typically exceeds the requirements of DOT and ECE. SNELL standards focus on multiple aspects, including higher impact tests, ensuring that helmets can withstand more severe impacts. They also conduct tests for shell penetration, retention system effectiveness, and peripheral vision, making SNELL-certified helmets some of the safest options available. Manufacturers choosing to meet SNELL standards are subject to regular and random testing, ensuring continuous compliance.
FIM Standards: The Fédération Internationale de Motocyclisme (FIM) standard is a relatively new addition, specifically designed for racing helmets. FIM certification combines rigorous impact testing with assessments of rotational forces, aiming to provide maximum protection for high-speed motorsport environments. Helmets that achieve FIM certification have undergone a comprehensive evaluation, including linear and oblique impacts, penetration tests, and visor resistance to ensure they offer the highest level of safety possible for professional riders.
The integration of materials plays a crucial role in enabling helmets to meet these diverse safety standards. Advanced materials such as composite fibers, carbon fiber, and Kevlar provide the necessary strength, flexibility, and impact resistance required to pass these rigorous tests. Simultaneously, innovations in helmet construction, such as multi-density EPS liners and rotational force mitigation technologies like MIPS, contribute to the overall safety profile of the helmet, aligning with SNELL and FIM objectives.
By understanding the implications of DOT, ECE, SNELL, and FIM standards, riders can make more informed decisions when selecting a helmet. It's important to consider the specific riding activities and conditions you'll face to choose a helmet that offers the best protection for your needs. Whether for daily commuting, casual riding, or professional racing, selecting a helmet that meets or exceeds these safety standards is crucial for ensuring your well-being on the road.
Core Helmet Materials Explained
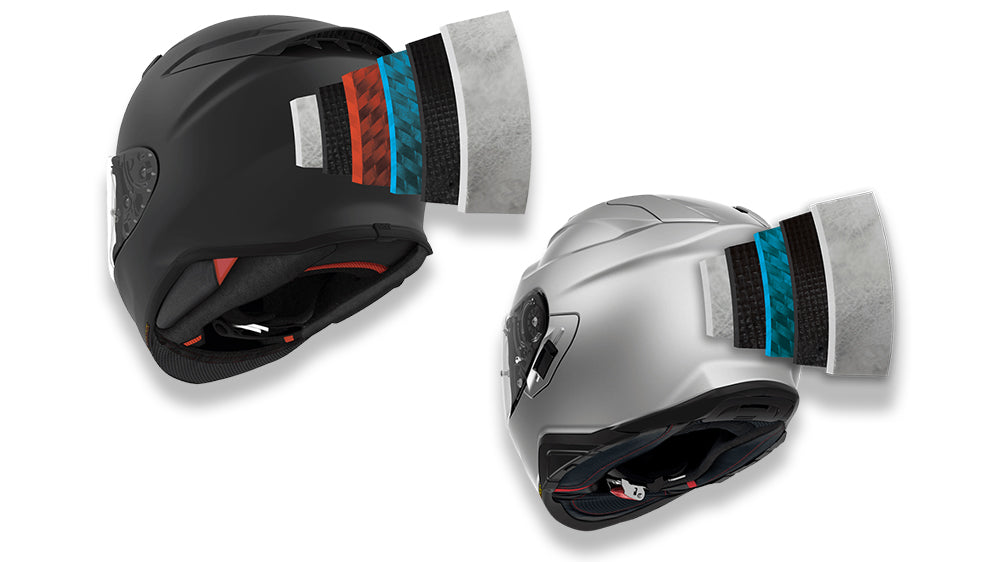
Innovations in materials and helmet construction have significantly improved motorcycle helmet safety over the years. With advancements in material science, manufacturers have integrated new materials to enhance protection, comfort, and durability.
Composite Fibers: The integration of composite fibers like carbon fiber, Kevlar, and fiberglass has been a game-changer in the construction of helmets. Carbon fiber is renowned for its strength-to-weight ratio, so carbon fiber helmets offer superior protection without the bulk. Kevlar, known for its use in bulletproof vests, adds unmatched tensile strength and flexibility, providing increased impact resistance. Fiberglass helmets, while slightly heavier, are favored for their cost-effectiveness and ability to disperse impact energy efficiently.
ABS and Polycarbonate: ABS (Acrylonitrile Butadiene Styrene) and Polycarbonate are widely used in helmet shells for their impact resistance and flexibility. ABS helmets are known for their toughness and are typically more budget-friendly, making them a popular choice for casual riders. Polycarbonate helmets, on the other hand, offer excellent resistance to impact and penetration, and when combined with other materials, can result in lightweight and highly protective helmets.
Advanced Thermoset Resin: This technology is a significant step in plastic helmet construction. Thermoset resins, when reinforced with fibers, create helmets that are not only lightweight but also extremely resilient to impacts. The thermosetting process results in material that is permanently hard and heat resistant, providing a stable and protective structure that doesn't degrade under environmental stress.
Innovative Construction Techniques: Beyond materials, innovative construction techniques such as in-mold technology, where the helmet's outer shell and the impact-absorbing liner are fused together in the helmet mold, have led to helmets that are lighter, stronger, and more durable. This method improves the energy absorption capabilities of the helmet, ensuring better protection for the rider.
Impact on Safety: These material and construction innovations have directly impacted helmet safety, allowing helmets to meet and exceed rigorous safety standards like DOT and ECE. By leveraging the unique properties of these materials, helmets can offer enhanced protection against impacts, penetration, and abrasion, significantly reducing the risk of head injuries in the event of an accident.
As material science continues to evolve, we can expect even more breakthroughs in helmet technology, leading to helmets that offer unprecedented levels of safety and comfort for riders.
Comparative Analysis of Helmet Materials
The choice of material in motorcycle helmet construction significantly influences its performance in terms of safety, comfort, and suitability for different riding conditions. Here's a comparative analysis of the primary materials used in the different helmet types:
Composite Fibers (Carbon Fiber, Fiberglass)

Product: Aria Corsair-X Kiyonari Motorcycle Helmet
Strengths:
- Lightweight and Strong: Composite materials offer an excellent strength-to-weight ratio, reducing neck fatigue without compromising protection.
- Impact Resistance: They have superior energy absorption properties, distributing impact forces to minimize injury.
- Durability: These materials are resistant to abrasion and environmental factors, ensuring longevity.
Weaknesses:
- Cost: Generally, composite fiber helmet prices are much higher due to the materials and complex manufacturing processes.
- Repairability: Once damaged, they are more challenging to repair compared to other materials.
Situational Best Uses:
- Racing: The lightweight and strong nature of composite fibers make them ideal for high-speed racing where performance and protection are critical.
- Long Rides: Their lightweight characteristics also benefit long rides, reducing rider fatigue.
Products Using Composite Fibers: Arai Corsair-X Motorcycle Helmet Line
ABS and Polycarbonate
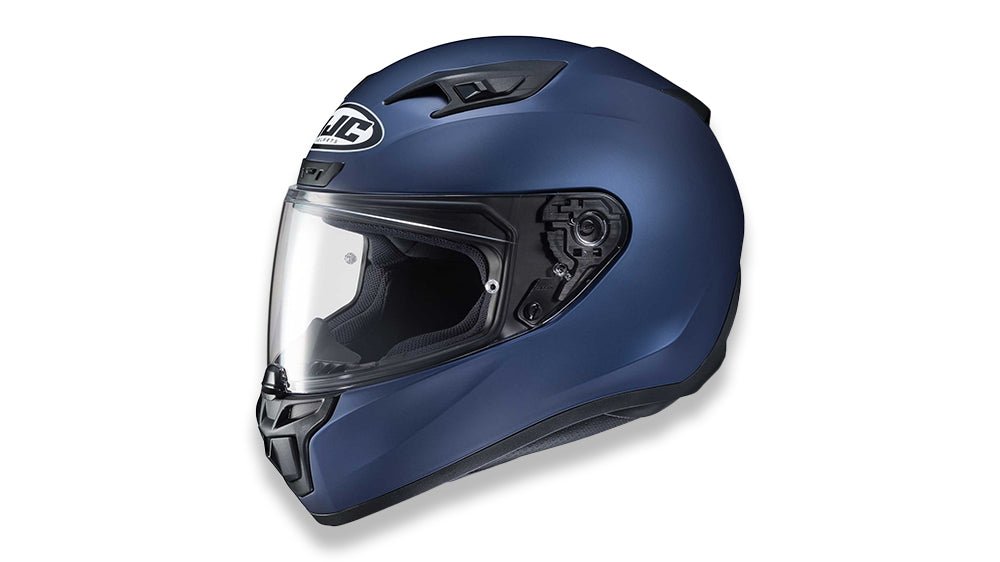
Product Pictured: HJC i10 Base Model
Strengths:
- Impact Resistance: Both materials offer excellent impact resistance, effectively absorbing energy.
- Cost-Effective: Helmets made from ABS or polycarbonate are generally more affordable, making them accessible to a broader range of riders.
- Versatility: These materials can be molded into various shapes, allowing for a wide range of helmet designs.
Weaknesses:
- Weight: Helmet weights tend to be heavier than composite fiber helmets, which might contribute to rider fatigue over long periods.
- Less Durable: While still durable, they may not offer the same level of resistance to abrasion and environmental degradation as composite materials.
Situational Best Uses:
- Everyday Use: Given their cost-effectiveness and good level of protection, these materials are well-suited for casual riding and everyday commutes.
- Beginner Riders: The affordability and adequate protection make them a good choice for new riders.
Prodcuts Using ABS and Polycarbonate: HJC i10 Motorcycle Helmet Collection
Advanced Thermoset Resin
Product Image: Fly Formula S Carbon Legacy Motorcycle Helmet
Strengths:
- High Impact Resistance: Thermoset resins, when combined with reinforcing fibers, offer excellent resistance to impacts.
- Lightweight: They provide a good balance of lightweight characteristics and strength.
- Heat Resistance: These materials do not melt or deform under high temperatures, maintaining their protective properties in various conditions.
Weaknesses:
- Cost: Like composite fibers, helmets made from advanced thermoset resins can be more expensive due to the materials and manufacturing techniques involved.
- Limited Repairability: Similar to composite fibers, repairing these helmets can be difficult.
Situational Best Uses:
- Professional Racing: The high impact resistance and lightweight nature make thermoset resin helmets suitable for professional motorsport environments.
- Adventurous Riding: Their durability and resistance to environmental factors make them excellent for off-road and adventurous riding.
Helmets that use Advanced Thermoset Resin: Fly Formula S Carbon Collection
Understanding the strengths and weaknesses of each material helps riders choose a helmet that best fits their specific needs, whether for racing, daily commuting, or adventurous riding.
Leave a comment